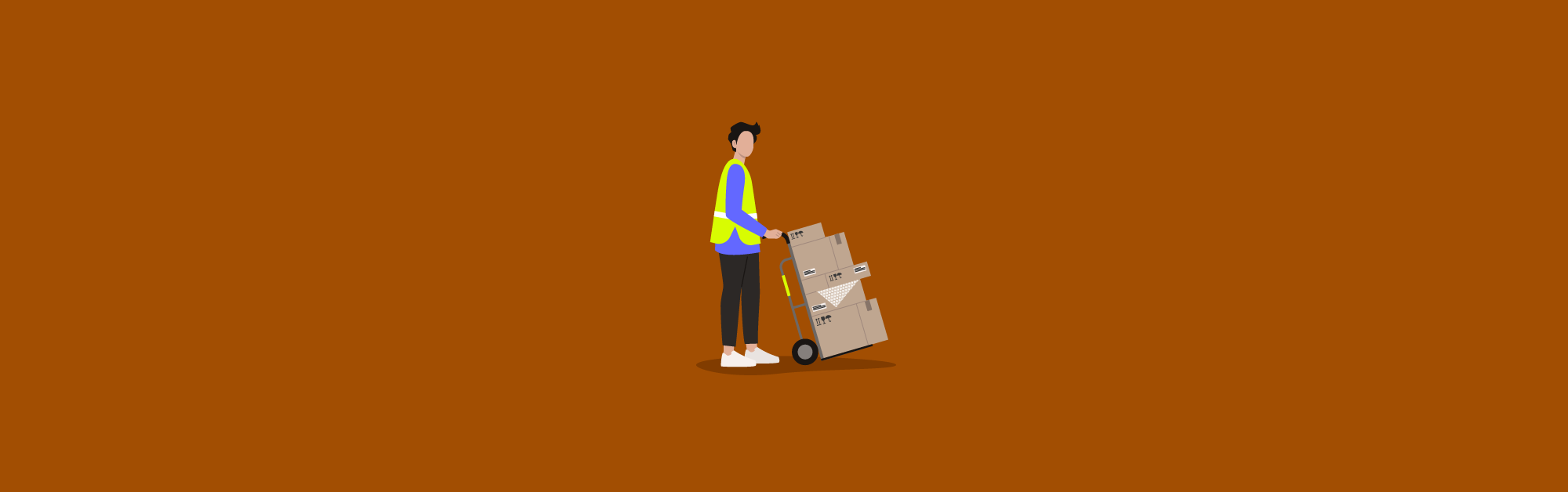
It may not be the sexiest part of your store, and it doesn’t get a lot of customer eyeballs, but your stockroom is still a critical part of your physical location.
In many ways, your stockroom acts as the headquarters of the store’s operations. It’s where your management office will be located, where you’ll receive shipments, where your staff will first discover the exciting new inventory, and where your extra stock will live.
Manage it right, and the stockroom will help you run a tight ship. But if you mismanage it? Your stockroom can leak its chaos out onto the floor of your store.
Here’s the good news: there are quite a number stockroom organization tips you can implement to set up your stockroom for success and keep it running at its peak.
Here’s how:
- Maximize your vertical space
- Place the most popular items near the front
- Keep heavy merchandise on or near the floor, but keep light merchandise completely off the floor
- Utilize inventory management software
- Invest in the right storage units
- Set up a system (and label it)
- Don’t neglect climate control the stockroom
- Provide excellent lighting
- Keep customers out of the stockroom
- Keep all necessary tools in the back (and label them!)
- Create an open shipping and receiving area
- Standardize organization across all locations
- Conduct regular training and audits
- Centralize your inventory data
Want to streamline stock control in your retail business?
Download this free inventory spreadsheet to help you better manage your stock, purchases and sales.
1. Maximize your vertical space
Don’t limit yourself to your floor space. Stockrooms typically have fairly high ceilings, so build up. The more items you can get onto higher shelves or racks, the more floor space you can free up for working staff to move in, which is always a plus. Invest in a few safe stools and ladders to make navigating the higher shelving easy.
As for how to maximize vertical space, one thing you can do is use shelving units that go up to the ceiling. That way, you can store more inventory without taking up additional floor space.
You should also consider stackable bins and containers to keep items organized and easily accessible. This is especially useful for small or lightweight items. For example, if you’re a toy store, you can use stackable bins to sort and store different sizes of stuffed animals or small trinkets, making it easy to find the exact item you need quickly.
2. Place the most popular items near the front
Help your floor staff function at peak efficiency by placing your most popular items near the front of your stockroom so they can quickly grab them and get back to the floor. While your employees will likely come to learn the stockroom by heart, delving into the back still eats up time and potential sales.
Nate Masterson from Maple Holistics suggests that you implement a policy of “forward space”. That is, keep a full box of your most popular products in easy reach, rather than just one or two. In practice, he says, “This can also mean taking two shelving slots instead of one if it’s selling twice as much as another item. Besides making it easier to run a shop, forward space can also help you simply track your sales trends.”
3. Keep heavy merchandise on or near the floor, but keep light merchandise completely off the floor
This is a safety tip: store your heaviest merchandise as close to the floor as you can. This will prevent potential collapses, but it will also lower the potential for injuries as your staff move the items around.
Conversely, lighter merchandise should be stored off the floor, so as to prevent cluttering and tripping. Cathy Donovan Wagner of Retail Mavens stressed that you should particularly keep clothing off the floor. Once she “found a dead mouse in a ‘return to vendor’ pile!”
4. Utilize inventory management software
Inventory management software is the perfect tool to help you keep your stockroom running at peak efficiency. For instance, a good stock control solution will help you accurately predict how much merchandise you’ll need shipped in and when, which will help guarantee your stockroom never becomes overstuffed and your floor never becomes understocked.
Inventory management software will also make it easy to run regular inventory counts. Kyle Baptist, the owner of Marconi’s Beach Outfitters, says that regular stock counts with a great inventory system (they use Lightspeed) “save time at the end of the season because you do not have to do an entire count.”
If you conduct inventory counts in the stock room, do yourself and your team a favor by adopting a mobile-friendly solution. That way, optimize the stock count process and reduce errors.
Scanner by Lightspeed is a great example of this. Scanner transforms your iOS or Android device into an inventory scanning tool so you can conduct full and partial inventory counts from anywhere in the store. You can also enable multiple team members to count items simultaneously, saving everyone time.
“The stocktake process for us used to involve a lot of spreadsheets, and this wasn’t ideal because it leads to mistakes. Now with Lightspeed, people can use devices to scan easily and update the stock record,” remarks Paul Stephens, Head of Data & Technology, Neal’s Yard Remedies.
5. Invest in the right inventory storage units
Type of storage | Ideal for | Best use cases |
Shelving Units | Larger, bulkier items that need to be easily accessible | Adjustable shelves for versatility |
Racks | Hanging items such as clothing or tools | Heavy-duty racks for heavier items |
Drawers | Smaller items that need to be organized and protected | Office supplies, small parts |
Bins and Containers | Sorting and storing items of various sizes | Stackable bins for small to medium-sized products |
Cabinets | Valuable or sensitive items that need to be secured | Lockable cabinets for extra security |
Mobile Storage Units | Dynamic stockrooms where the layout needs to change frequently | Seasonal items, products that need frequent movement |
There are many different types of storage units available to someone outfitting a stockroom. Shelving, racks, drawers, bins, cabinets, etc. The exact type(s) that will work for you will depend on your stock, of course, but it’s recommended that you invest in mobile storage units right from the beginning.
Mobile storage units allow you to maximize the space in your stockroom between the walls with storage that can move around.
So, how do you decide which types of inventory storage equipment are right for you? Start by looking at the types of products you need to store:
- Shelving Units: Ideal for larger, bulkier items that need to be easily accessible. Use adjustable shelves for versatility.
- Racks: Perfect for hanging items such as clothing or tools. Choose heavy-duty racks for heavier items.
- Drawers: Best for smaller items that need to be kept organized and protected, such as office supplies or small parts.
- Bins and Containers: Useful for sorting and storing items of various sizes. Stackable bins work well for maximizing vertical space and organizing small to medium-sized products.
- Cabinets: Great for valuable or sensitive items that need to be secured. Lockable cabinets can provide extra security.
Mobile Storage Units: Versatile for dynamic stockrooms where the layout needs to change frequently. They are excellent for seasonal items or products that need to be moved around often.
6. Set up a system (and label it)
One key to a functioning stockroom is creating an organized system for where you place items. Whether you choose to separate your products by department, color, size, style, etc. is up to you, but pick a way and stick to it.
A women’s clothing store, for instance, could choose to divide the stockroom by petite and misses sizing. Those sections can then be categorized further by knits and denim (which need to be folded) and dresses, blouses, and trousers (which need to be hung).
Once you’ve picked your system, stick to it and label it, especially if you have a large stock room.
7. Don’t neglect climate control the stockroom
Climate controlling your stockroom is essential because it helps keep all of your products in pristine condition. But it’s also really important because you’re going to have employees working long hours back there.
A broken A/C system can make employees miserable during the summer months, which in turn, can prevent them from showing up as their best selves on the sales floor.
8. Provide excellent lighting
It’s easy to forget the lighting aspect of your stockroom. After all, customers aren’t going back there. But a well-lit stockroom is important for a number of reasons.
- Your staff needs good light to work by. Good lighting creates a safer environment for them, and it will also help keep them awake. Remember, inventory work can be cumbersome and you don’t need a melatonin boost from low-lighting to help you fall asleep in the stockroom.
- Good lighting makes it harder to lose items in the back. With poor lighting, it’s easy for items to slip into cracks and crevices never to be heard from again.
9. Keep customers out of the stockroom
You’d think that customers don’t want to go in the stockroom, right? However, you’d be surprised at the number of shoppers who would wander into the area—something that must be avoided as much as possible.
Stockrooms can be somewhat dangerous and can open you up to all sorts of negligence lawsuits if a customer gets hurt back there. It also opens you up to the possibility of loss of your stock or your employees’ items. Best to keep them out. Plus, no one really wants to see how the sausage gets made.
10. Keep all necessary tools in the back (and label them!)
A lot of stuff is going to happen in the back. Unboxing, boxing up, folding, printing, retagging, etc.
You need to make sure all the necessary tools are in the back from box cutters and tagging guns to staplers and hole punchers. Wagner also suggests “clearly [tagging] all office supplies that are used in the back room so that it is obvious that they are to be returned there if found elsewhere in the store.”
11. Create an open shipping and receiving area
Your store needs somewhere to receive and unbox all your shipments and there’s no better place than the stockroom. Set up a desk by the door at a comfortable folding height, and reserve a fairly large, clear area where boxes can be placed and stock easily removed.
The tighter your shipping and receiving space is, the harder it will be for your stock employees to do their jobs, so give them as much space as you possibly can. One method for maximizing this space is to utilize mobile collapsible bakers racks that can be set up when you really need the extra storage space and taken down at all other times.
12. Standardize organization across all locations
If you run multiple retail stores (and assuming they all have similar formats) create standard operating procedures for your stock room and enforce them across all your locations.
For example, you can implement a standardized labeling system for shelves and bins. Or, you could establish uniform guidelines for inventory rotation and stock replenishment.
In doing so, you promote consistent and efficient workflows so your stockrooms can run smoothly. From a workforce perspective, these SOPs also make it simpler for staff to work interchangeably between locations and reduce errors or confusion.
13. Conduct regular training and audits
If you have complex stockroom operations, it may help to train your teams and ensure they are familiar with the latest procedures and best practices. One tip is to schedule periodic refresher training sessions and conduct random audits to identify any areas that need improvement.
Let’s say, you notice that staff frequently misplace inventory due to inconsistent labeling. You conduct a random audit and identify this issue and then schedule a refresher training session focused on proper labeling techniques and inventory placement. This ensures everyone is on the same page and reduces future errors.
14. Centralize your inventory data
Use a centralized inventory management system to track stock levels, movements, and needs across all locations. For best results, choose a system that gives you real-time inventory data. That way, you always have a handle on what’s in stock (and what’s not) and then make the right calls based on that data.
Let’s say one of your stores experiences a sudden surge in demand for a particular product. With real-time inventory data, you can quickly identify which other locations have excess stock of that product and arrange an inter-store transfer to meet the demand without overstocking or running into shortages.
Thes systems ensure that stores don’t have too much product sitting in their stockrooms or warehouses—which ultimately leads to more efficient operations.
Lightspeed’s Advanced Reporting capabilities provide robust inventory reports such as:
- Inventory summary
- Replenishment
- Performance
- Dusty inventory
- Sell through
- Recently out of stock
- Inventory types reports
Equipped with this data, you and your team can make informed decisions about purchasing, stocking, and transferring inventory, leading to optimized stock levels, reduced waste and increased sales efficiency.
Wrapping up
By starting with an organized foundation and implementing a few key policies, you can make sure that your stockroom functions with smooth efficiency, rather than becoming a chaotic black hole you try not to think about.
Maximizing efficiency in your warehouse is key to maintaining a competitive edge. Explore our Warehouse Efficiency Tips to discover actionable insights that can help you streamline processes, reduce errors, and improve overall productivity.
Using a robust retail and inventory management software (like Lightspeed) can also keep the products in your stockroom in check.
Want to see how our solution can help you manage your stock with ease? Watch a demo of Lightspeed today!
FAQs
How to organize your stock or inventory?
Organize your stock by categorizing items, labeling everything clearly and using shelving and bins for optimal storage. You can also implement the First In, First Out (FIFO) method for perishable items and perform regular inventory audits to ensure accuracy and efficiency.
How to store inventory in a small space?
Maximize small storage spaces by using vertical shelving units, stackable bins and compact modular storage solutions. Optimize the layout to ensure accessibility and use mobile storage units to allow flexible space utilization as needed.
How do you organize a stockroom?
Organize a stockroom by standardizing the layout, categorizing products and labeling everything clearly. Utilize inventory management software to keep track of stock and conduct regular maintenance to ensure cleanliness and organization.
How to organize an inventory list?
Organize an inventory list by categorizing items, using descriptive names, and implementing a numbering system such as SKUs or barcodes. Regularly update the list to reflect current stock levels and consider using digital inventory management tools.
What is your method for sorting and storing inventory?
Sort and store inventory by categorizing items, labeling clearly, using appropriate shelving units, and implementing the FIFO method. Utilize technology like barcoding and inventory management systems for efficient tracking.
How do you maximize inventory space?
Maximize inventory space by using vertical storage solutions, optimizing the layout, utilizing stackable bins, investing in compact modular storage systems, and regularly reviewing and reorganizing the space for efficiency.
How do you organize household inventory?
Organize household inventory by categorizing items, labeling containers, using shelving, and potentially using an app for digital tracking. Regularly check and update the inventory list to maintain organization.
How do you arrange inventory?
Arrange inventory by categorizing similar items together, labeling clearly, using shelves and bins, implementing the FIFO method for rotation, and maintaining regular reorganization for efficiency.
How do you organize inventory shelves?
Organize inventory shelves by grouping similar items, using clear labeling, adjustable shelves for different sizes, placing frequently used items at eye level, and regularly reorganizing for efficiency.
How do you keep track of stock inventory?
Keep track of stock inventory using inventory management software, conducting regular audits, implementing barcoding or RFID systems, ensuring real-time data updates, and following consistent tracking procedures.
What is the best way to categorize inventory?
Categorize inventory by grouping items by category, type, use, or alphabetically, and use numerical systems like SKUs for precise tracking. Choose a method that best suits the nature and size of the inventory.
How do you arrange inventory?
Arrange inventory by categorizing items by type, using shelves and bins, labeling clearly, implementing the FIFO method, and regularly updating the arrangement to maintain efficiency and order.
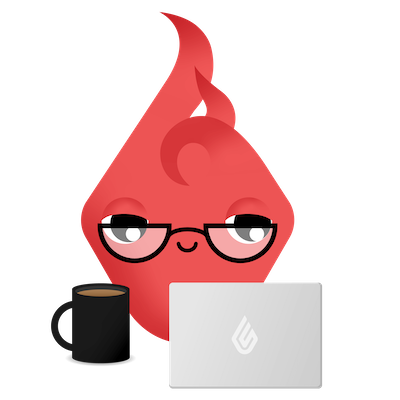
News you care about. Tips you can use.
Everything your business needs to grow, delivered straight to your inbox.